David P. Anderson 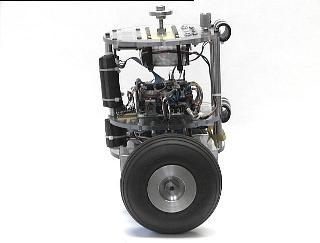
I've been working on a two-wheeled balancing robot,
nBot .
This robot was featured as
NASA's
Cool Robot of the Week for 19 May 2003. Thereafter Scientific American's online website,
SCI/Tech Web Awards, honored the NASA page as one of the top 10 engineering and technical web sites for 2003, referencing nBot in its text. nBot is also featured in a new O'Reilly book spun off from Make Magazine in 2006, called
The Makers.
The basic idea for a two-wheeled dynamically balancing robot is pretty simple: drive the wheels ...
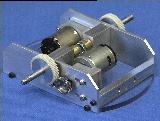
The robot hardware was built in my home machine shop. Here as some
exploded views of the motor platform and drive components, as well as the castering tailwheel, now removed, which was used for testing and calibrating the motors and encoders before
nBot was able to balance on two wheels. The robot uses the
HC11 robot controller developed for the
M.I.T. 6.270 Robotics Course, the same robot controller used on the
LegoBot and
SR04.
Rev 1. This began as an experiment to learn to control an
inverted pendulum. I began with a
three wheeled robot with a
ball-bearing pivot used to attach a 3 foot wooden pole topped with an orange Nerf Ball. The pivot has a low-friction 5k potentiometer used for measuring the tilt angle of the pole. I moved the
battery pack over the rear wheel to give more stability. Here is an
mpeg movie (10 Meg) of the robot balancing the pole in my office.
Here (3.3 Meg) is a shorter version, and
here (3.7) is another.
Rev 2. After learning to balance the pole, the robot was re-built as a
two-wheel version, with the battery mounted directly above the wheels. The ball-bearing pivot was attached to the bottom of the robot with a
short aluminium feeler touching the floor. In this way the robot can sense it's angle to the floor and, assuming the floor is level, to gravity as well. The aluminium feeler has a teflon pad on the end to help it ride over cracks and joints in the floor.
Rev 3. For the third version a third deck was added and the batteries moved to the
top deck. This allows the robot to generate more torque without having to tilt over as far. The
side view of the platform shows the battery and user interface on the top deck, the microcontroller and h-bridge on the middle deck, and the motors...
Visit Site